How Silk is Printed
By Drake's
Jul 13, 2022
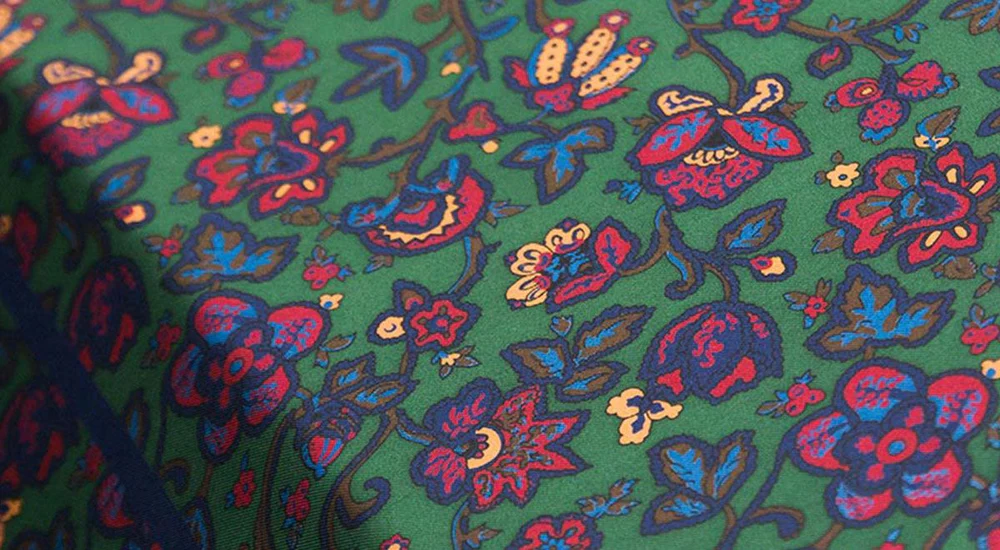
Go behind the scenes and discover the intricate craft that goes into our printed silk ties, pocket squares and scarves.
The Drake’s ethos has always been built around creating product that’s as good as we can possibly make it. There’s nothing that epitomises that philosophy better than the process behind our printed silks; the material for which we might be best known for. Appreciating an elegant design is one thing, but to truly comprehend the work and the craftsmanship that goes into each of our prints, you need to understand how those designs got there.

We’re very lucky to have our printing mill located in the ancestral home of the British silk industry, Macclesfield. The mill has been in operation for almost two hundred years, and that accumulated expertise is what shines through in the final product. Macclesfield is located in a natural basin, and blessed with especially soft water. It was this softness that led to the settlement of the silk industry, as soft water is incredibly important for the washing and treatment of the silk. “We’d probably be the only mill left in the world with it’s own, usable mill pond, which we use for all of the processes here” says Steve, one of the mill’s directors. “The river runs through the property - there actually used to be a waterwheel here as well. The waterwheel used to run the machinery. It was completely self-sufficient for a long time, and to a certain degree still is. We don’t make tea with it though!”

The foundational step in the printing process is the creation of the dyes, all of which are made and mixed on site. “We’re dyers, printers and finishers so we do the whole thing”, says Steve. “That’s quite unique to us here. We mix our own colours and everything is geared up to our own color book and dye recipes.” That allows us incredibly fine control over colour - essential when working with some of the intricate designs Drake’s is known for.

The silk arrives at the mill as ‘grey goods’ - woven, but undyed and untreated. Before the printing begins in earnest, the grey goods must be piece-dyed. This is done using a specialised dying machine that runs the roll of silk back and forth through a dye bath. “We wash fabric with the full width outstretched for as long as we possibly can throughout the whole process. A necktie needs to be a pretty much perfect level of dying as any creases will be obvious in the final product.” Each dye bath has a specific amount of dyestuffs in it, relative to the amount of cloth being dyed. As the cloth winds back and forth through the bath, this dyestuff gets exhausted as the cloth absorbs the colour. When it’s all gone, the cloth will match the desired colour and shade. After drying, the cloth is run through a stenting machine, which corrects it’s warp and weft and ensures the cloth is perfectly straight. From there, it’s sent to the print room.
Before printing can begin, the printing screens must be prepared. Essentially large wooden frames stretched with mesh, the screens are sent through an engraving machine which applies a negative of the design to the mesh via wax jet. The amount of screens required for a single varies depending on how many colours are required. An intricate design might need to be hand-printed half a dozen times or more, using as many separate screens. “We start off usually with the black filetto, and then build the design up from the smallest print area up to the largest area of that particular design.”
The silks are laid out on enormous, twenty-two meter long tables. Working in pairs, the printers slowly move down the length of the silk, printing a screens worth of the cloth and then continuing down. “The screen is engraved with the negative omitted from the screen” says Steve, “so when the two guys push the colour from one side of the screen to the other, they push the colour through the negative area, thereby printing the positive area.” To avoid contaminating the design, the printers print every second space on the length of cloth, before coming through and doing the spaces between. “They’ll print spaces one, three, five, seven and so on down the table. When that’s dried slightly, as they’ve gotten to the other end of the table, they’ll come in and fill in the even numbers. So you’re not printing each screen right next to each other all in a row. You’re not getting the frame hitting wet areas of the design and leaving marks. So when they come through with the next colour, the areas either side won’t be affected. "

The dye process leaves the silk looking dark and brittle - a far cry from the rich and delicate colours the final product will have. “These colours haven’t developed yet”, says Steve. “These are basically just the printed colours. It won’t be until these pieces have actually been dried and steamed that we will see the true colour.” This is due to the traditional dye and discharge method the printers use. “So the fabric is dyed into the ground colour, and then when the colour is applied to fabric and it’s steamed, there’s a chemical in that colour that destroys the ground and replaces it with the decoration colour. You’re not printing on top of the fabric, you’re actually printing into the fabric. You’re discharging the colour into the fabric as opposed to printing on top of the fabric.” After every printing process once down the table the excess colour is washed away and then the screen is dried, ready for the next colourway.
Once the printing has been completed, the cloth is steamed in order to discharge the dyes, before being washed again to remove any excess colour. This involves placing the cloth on a special winch machine, which feeds it back and forth through a solution of water and a special soap. The excess colour will be washed away. After that it gets dried and inspected before being stented again and having it’s finish applied.

The final, rather ominous sounding step, is known as ‘breaking’, and it’s actually integral to achieving the soft handle of the finished product. Breaking essentially involves feeding the roll of cloth back and forth through a special machine, made up of a series of wooden rollers, each fitted with brass buttons. “It’s an old machine as you can tell, but we would never replace something as good as this”, explains Steve. “The fabric intertwines between each roller and the machine runs backwards and forwards; essentially beating the fabric. When the other processes are finished you do get a little bit of crispiness in the fabric, so this starts to break down the fibres within the fabric and gives it that final, soft feel. We might go once down and once back again, we might do a second or third time. It depends on what kind of softness you want.”
With that, the silk is essentially complete, and ready to be shipped from the mill to our Haberdasher Street factory, which it will be painstakingly cut, sewn and assembled by hand, by an entirely different team of skilled craftspeople. Making truly beautiful things is never easy, and it’s certainly not quick. But we think the results are worth it.